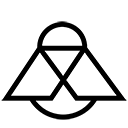
Complete CAM solution for Rhino + Grasshopper
Woodbee is a compact CAM plugin for Grasshopper currently focusing on the milling objects from planar sheets. The tool can automatically detect different features in the input geometry and suggest suitable milling strategy based on the given tool and machine type (3 axis to 6 axis machines). Once the tool path is generated it can be simulated in Rhino viewport in real time. After a successful simulation, the tool path can be converted to GCODE or KUKA command using the specified postprocessors.
Buy Woodbee
License Types
We offer various license types for Biber , catering to different needs and durations. Before choosing the most suitable license for your requirements, let us introduce you to the available options:
IMPORTANT NOTICE
Always download latest version of Woodbee.
Please remember that all licenses will not be renewed automatically. To continue using Woodbee beyond the license’s expiration date, users must renew their licenses before that time.
Additionally, we highly recommend considering the Professional License or licenses with longer durations, as we may introduce more features to the software in the future. Purchasing a longer-duration license ensures you have access to these new functionalities without incurring any additional costs.
Learn Woodbee
Version Log
Version 1.0.5.0
Initial verion (this is a Beta version valid till 30/12/2022)